When creating custom plastic enclosures, whether for electronics, consumer products, or industrial equipment, the manufacturing process you choose profoundly impacts design requirements. One of the most widely used manufacturing methods for plastic enclosures is injection molding. However, the injection molding process has its considerations that designers must navigate to achieve functional and aesthetically pleasing results.
You may be developing an enclosure for a new consumer electronics device. Or the façade of a new electric vehicle (EV) charging station. Maybe it’s next-gen emergency medical equipment used by EMTs and hospitals; it doesn’t matter. Ferriot has a great deal of design experience with custom injection molded enclosures. When designing a new product, it is essential to consider several key factors when using an injection molded custom plastic enclosure, regardless of the final application.
The Ferriot team has years of experience in the custom injection molding industry. Logically, tapping their knowledge and expertise in new enclosure development makes sense. This article provides valuable insights into successfully completing your new enclosure design while balancing form and function.
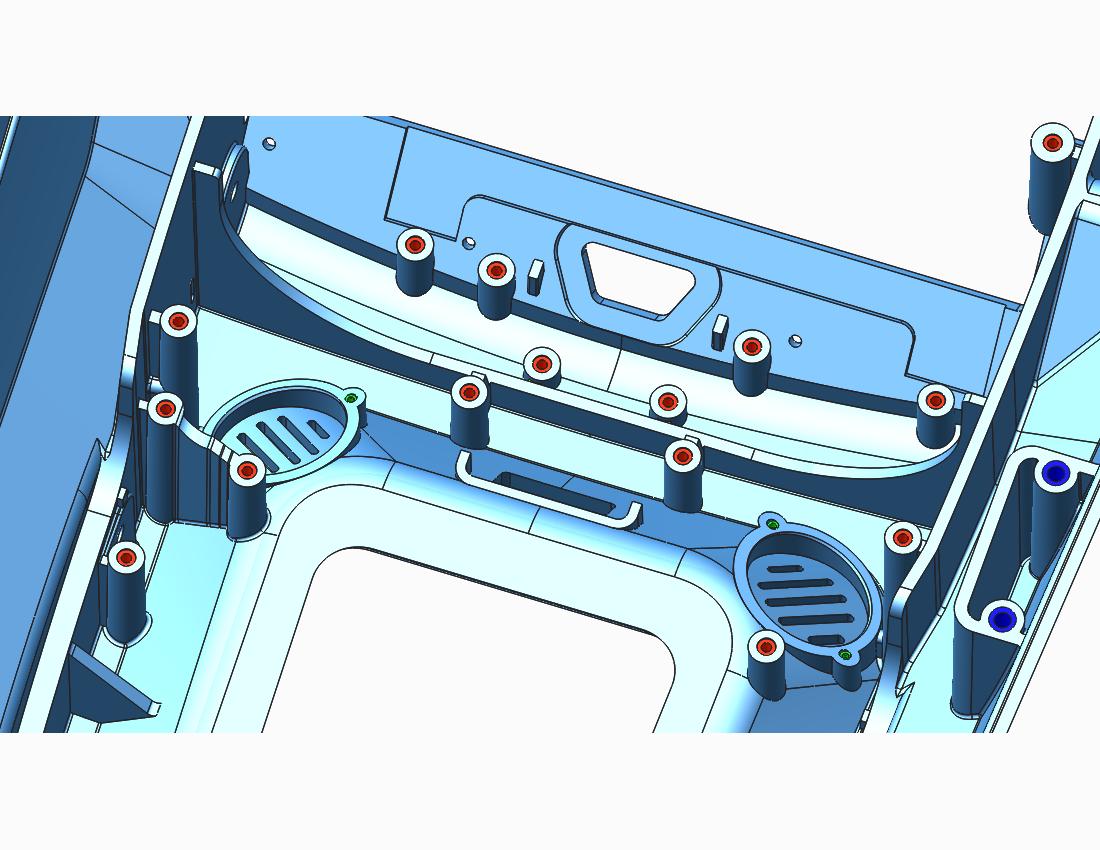
Design considerations for custom injection molded enclosure design include wall thickness, ribs and reinforcements, corners and fillets, and undercuts
Considerations for New Custom Plastic Enclosure Design
The User Experience
Critical to the success of any new product is having a thorough understanding of how the user interfaces with the enclosure, the mating components used during assembly, how all the pieces and parts fit together, and how much interference or clearance exists in those areas.
If the equipment is to be serviced or maintained, the designers must determine where access to interior components is needed. This data enables the team to start thinking about the necessary tolerances and if there are areas of risk. Sometimes, the product designer needs to be sure of how things will work, or even if it will work, within the current design. Then, the team reviews the option of building prototypes to test these unknowns, especially for any risky areas. Prototyping is always a good idea to test the feasibility of the design before going too far.
Design for Manufacturing (DFM)
Tooling engineers will utilize your product design and inputs to design tooling to manufacture your enclosure. To optimize production and part quality, the tooling engineer must consider several design features for the mold, from gate placement to surface finish.
Gate Placement: Where It All Begins
The gate, the entry point for molten plastic, is pivotal in how material flows into the mold cavity. Gate placement is more than just a technical consideration—it affects material wastage, defect potential, and the part’s visual appeal.
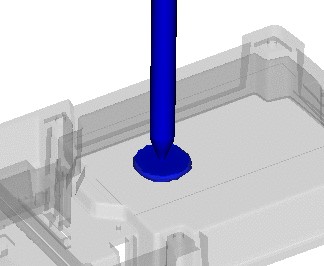
Defining gate placement in the custom injection mold design
Wall Thickness: The Key to Structural Integrity
Uniform wall thickness is a cornerstone of successful injection molding. It ensures even cooling and reduces the risk of defects such as warping and sink marks. Maintaining consistent wall thickness throughout the enclosure ensures structural integrity and contributes to a polished final product.
Strength in Ribs and Reinforcements
Enhancing the plastic enclosures’ strength without compromising material usage is a challenge that can be addressed through thoughtful rib and gusset placement. By strategically adding ribs to specific areas of the enclosure, designers can prevent flexing, warping, and deformation, all while optimizing material distribution.
Smooth Corners and Fillets for Durability
Sharp corners might look sleek, but they often lead to stress concentration points and potential cracks. To mitigate these issues, incorporating rounded corners and fillets boosts part strength and reduces the risk of defects during molding.
Navigating Undercuts and Complex Features
Undercuts, or features that prevent part ejection, can complicate the mold design. Addressing undercuts effectively or designing them to be mold-friendly is a strategy that simplifies tooling and minimizes costs. This balance between complexity and manufacturability is vital.
Surface Finish and Texture: Practical and Aesthetic Impacts
The texture of the mold’s surface transfers to the final part. Designers have the freedom to choose from an array of surface textures, but they must carefully weigh how these textures influence aesthetics, grip, and part release.
Material Selection: A Delicate Equation
Choosing the right plastic resin is crucial. In addition to necessary properties such fire or chemical resistance, one must understand how the resin reacts to the molding process. Different materials exhibit varying shrinkage rates during cooling and solidification. Designers must select materials compatible with the injection molding process and account for this shrinkage when determining dimensions. It is crucial to start the resin material selection process based on the standards and compliances your product must meet.
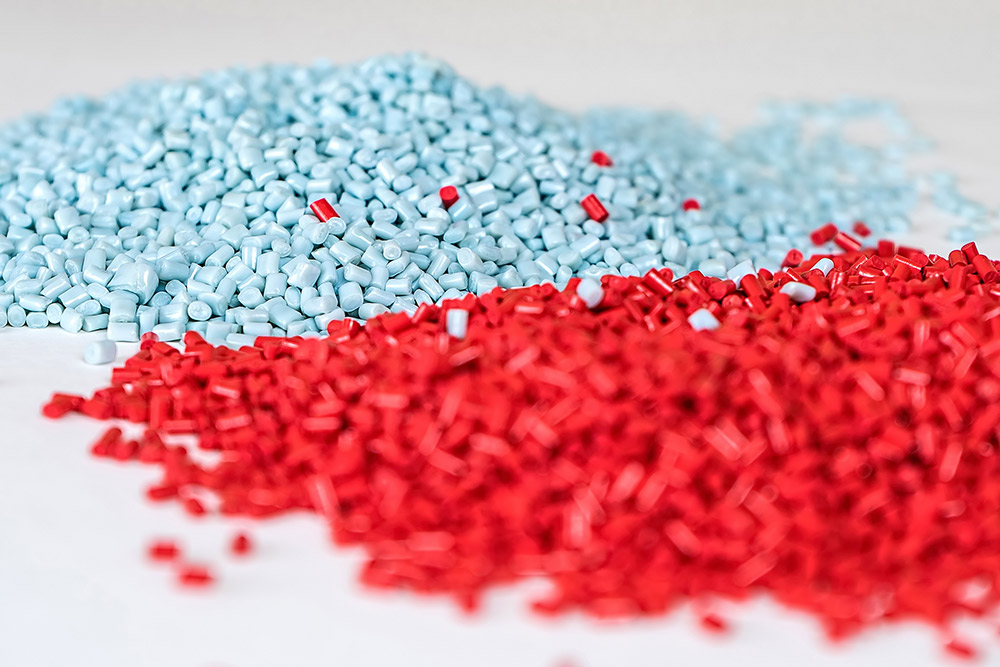
Material selection requires multiple considerations
One example: If you’re designing a medical device that needs to be near or in an MRI machine, it cannot have any metal whatsoever in the enclosure, including any metal inserts. That could be very dangerous inside an MRI machine.
An additional consideration when designing a medical device enclosure is the importance of EMI/RFI shielding. Design engineers must take care to ensure that their device doesn’t emit signals and that it meets various EMI-RFI shielding standards. If reducing RFI through design isn’t possible, engineers can use an RFI-shielded enclosure as an effective solution.
RFI shielding can be applied internally to electronic enclosures as a spray. This coating spray is often used in plastic enclosures to reduce interference effects. (See Understanding EMI / RFI Shielding for Injection Molded Components to learn more.)
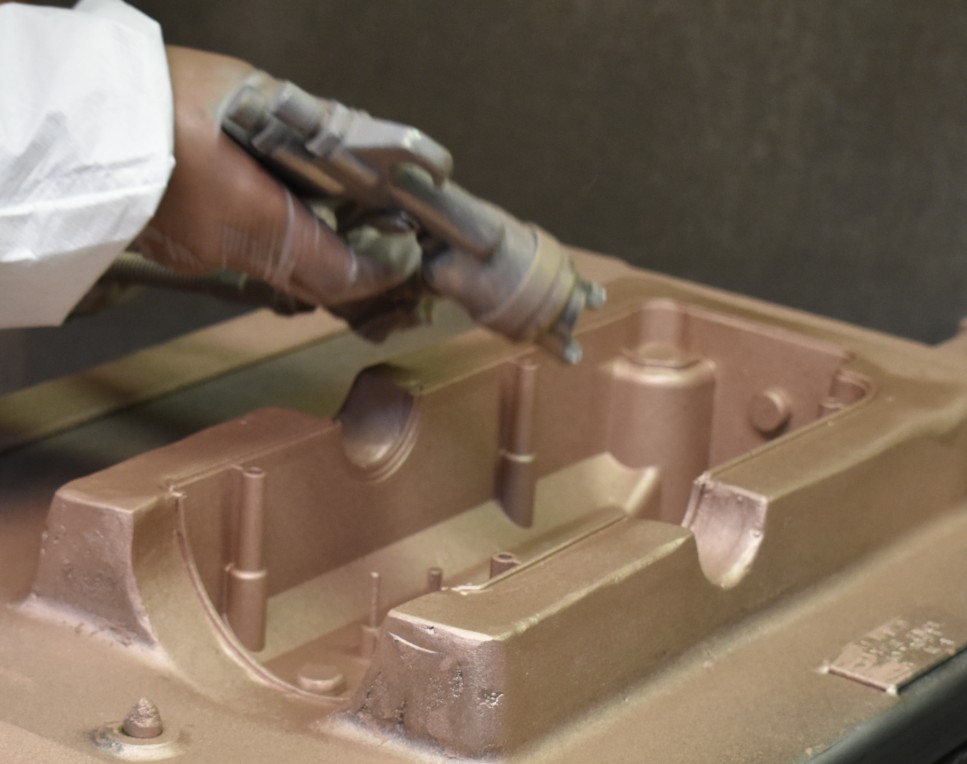
EMI/RFI shielding application to custom injection molded part
Once you have narrowed the resin selection, Ferriot’s supply chain team can work with you to determine its availability. The purchasing team researches where the materials are readily available, finding the best combination of price and delivery. We work hard to find the best possible price for the best quality materials that meet the enclosure’s design criteria. It helps narrow the material selection, so we provide a list of the appropriate materials and let you, as the customer, make the final decision.
Striking the Balance of Mold Complexity
Complex molds with intricate features might unlock design possibilities but also increase tooling costs and production time. Striking the right balance between design complexity and manufacturability is critical to ensure feasibility and cost-effectiveness.
Integration of Assemblies: Beyond the Mold
A well-designed enclosure isn’t just about what comes out of the mold. Designers should evaluate how different enclosure components fit together and how they can efficiently assemble them post-molding. Considerations include features like snap-fits, screw bosses, and alignment guides.
Tolerances: The Fine Print of Design
Though injection molding is extremely precise, it is necessary to account for variations in material shrinkage, mold wear and other factors during the manufacturing process that affect part size. Design and quality teams will determine acceptable tolerances which define the acceptable size variations for certain part features and overall dimensions. Tolerances allow for variation while ensuring that the part will still function and mate with other parts.
The Role of Moldability Analysis
Harnessing the power of computer-aided design (CAD) software to conduct moldability analyses is a smart move. This process identifies potential issues early on, allowing for necessary adjustments before the costly tooling stage.
FDA Requirements for Medical Devices
Understanding the FDA requirements for medical equipment is imperative to help decide the correct material selection and design controls. Then, knowing the product requirements, UL, flammability ratings, impact testing, and chemical and UV resistance is next. The product designer must prioritize these requirements, so the custom injection molder knows the most important ones. Then, our manufacturing engineering team will focus on hitting those requirements.
Summary
As you can see, developing a new enclosure requires much consideration. Designing plastic enclosures for injection molding is a delicate balance between aesthetics, functionality, and manufacturing feasibility. The considerations outlined are essential guideposts that steer designers toward creating enclosures that look great and result in efficient production using injection molding. Collaboration between designers, engineers, and manufacturers is the key to unlocking the full potential of this manufacturing process while delivering exceptional products to end-users.
The Ferriot team is here to support you in developing the right enclosure design that provides the proper form, fit, and functionality in a highly durable and attractive package. Based on the part geometry, complexity, and numerous other design factors, we work closely with you to develop the best custom injection molded solution for your new product’s design.